Petrochemical Industries
Petrochemicals Industry Structure and Characteristics
The petrochemicals sector is capital-intensive, highly competitive, and characterised by tremendous technological innovation. The sector makes up about 10% of the entire petroleum industry in terms of production quantities. However, the petrochemicals industry makes up a bigger portion of the overall industry when measured by product value, indicating the higher value of petrochemicals relative to fuels.
In the past, technological advancement in the advanced industrialised economies gave rise to the industry. Petrochemical production was centred in Western Europe, the US, and Japan up to the last part of the 20th century. However, manufacturing has significantly grown over the past three decades in regions with feedstocks that are priced competitively.
Fundamentals of the Petroleum Industry
Oil and gas production gave rise to the petrochemicals business by adding value to low-value by-products that had no application in the fuels sector. Plastics, synthetic rubber, solvents, fertilisers, medicines, additives, explosives, and adhesives are only a few of the important goods produced by the sector today. Almost all facets of contemporary civilization can benefit from the use of these materials. To mention a few typical uses, petrochemical chemicals are used in automobiles, packaging, household items, medical devices, paints, textiles, and building supplies. The capacity to process various kinds of raw materials and new technology are two more ways that the sector keeps up with innovation.
These raw materials are put through a number of processes in an effort to produce a small number of chemical building blocks. To create the finished petrochemical products, these building blocks are subsequently processed through a number of processes.
Compared to refined goods and natural gas, the target markets for petrochemical products are smaller and more niche. Even though petrochemical products often sell for more money than natural gas and refined goods, marketing is more difficult. As a result, market risks and competitive analyses are key factors in lenders’ evaluations of petrochemical project finance transactions.
Effluents from Petroleum Industry
According to Jain, Sharma, Dureja, Sarma, and Lal (2017), the petrochemical sector generates wastewater that is replete with complex organic compounds that are harmful by nature called hydrocarbons. These industries’ wastewater discharge has an impact on groundwater sources as well as freshwater ecosystems (Flörke, Bärlund, van Vliet, Bouwman, & Wada, 2019). The industries that create fuel, lubricants, and other petrochemical-based goods, as well as refine crude oil, are the main producers of petroleum industry effluents. According to the research findings, the oil sector will continue to produce and release effluents into the major water bodies. The effluent contains pollutants that are recognised to pose significant hazardous risks to the environment. The effluents produced by petroleum refineries vary depending on the type of oil being processed, the layout of the plant, and the operational techniques used (Noor & Mutamim, 2017).
The petrochemical sector. India will be the sixth-largest player in the global petrochemical industry by 2022, with a market worth over USD 190 billion. Strong macroeconomic foundations and population expansion in India are key facilitators for the country’s petrochemical manufacturing sector.
The Petrochemical Industry Soars
In the 1800s, kerosene, a fuel for cooking and warmth, was the main output of the petroleum industry. Petrol was viewed by refinery owners like Rockefeller and others as a wasteful byproduct of the distillation process. However, everything changed around 1900 when kerosene lamps were replaced by electric lights and cars entered the picture. Additionally, new petroleum fuels were required to run the World War I-era ships and aircraft. Following the war, more and more farmers started using tractors and other oil-powered machinery. The industry rapidly expanded in the 1920s and 1930s as a result of the rising demand for petrochemicals and the accessibility of petroleum and natural gas. Many chemical firms, such as Dow and Monsanto, entered the market.
Huge quantities of oil were produced and used as fuels and lubricants during World War II. United States
More than 80% of the aviation fuel used by the Allies during the conflict was provided by states. In addition to synthetic rubber, toluene (a component of TNT), pharmaceutical oils, and other essential military supplies, American oil refineries also produced them.
Applications
Plastics: A Petrochemical Gold Mine
After World War II, there was an even bigger increase in demand for petroleum products. From over 1.75 billion barrels in 1946 to almost 2.5 billion barrels in 1950, the United States used a lot more petroleum. Petroleum had supplanted coal as the nation’s primary fuel by the early 1950s. And the main cause was plastic.
Our expertise in the field
The largest consumer of plastics is the packaging sector, which makes up nearly one-third of all American manufacturing. Second in importance is the construction sector, which makes products like insulation, moulding, pipes, roofing, siding, and door and window frames out of plastic. Plastics are used extensively in a number of other industries, including the manufacture of cars and trucks.
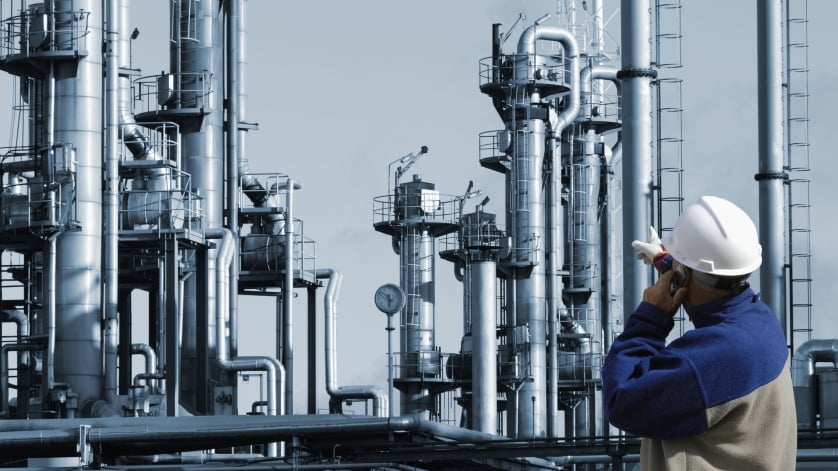
The Petrochemical Industry Slowdown
The environmental movement, which emerged in the 1960s and 1970s, made Americans leery of polluting companies, with the petrochemical sector being the main target. A slowdown was a result of opposition to the sector. The development of the petrochemical industries in Europe and Japan, a natural gas shortage.
Our expertise in the field
The petrochemical industry underwent a slow but steady reorganisation in the 1980s and 1990s as individual production facilities were bought or refinanced and chemical firms underwent reform. The goal of these mergers was to improve the standing of the major petrochemical corporations, including Shell and Mobil, in the market.

The Geography of Petrochemicals
In more than a hundred countries, there were nearly a million oil wells by the last decade of the twentieth century. more than 20 billion barrels are produced annually. The Middle East is thought to have roughly 41% of the world’s total oil reserves, and most experts regard Saudi Arabia with having the biggest original oil endowment of any nation.
Our expertise in the field
Eastern Europe is also rich in oil due to the massive resources in Russia. Under the North Sea, most of Western Europe’s oil is located. According to popular belief, 77 percent of the world’s recoverable oil has already been found. If so, it might be more expensive to discover and recover the remaining 23%, which are generally found in smaller fields or in harder settings.
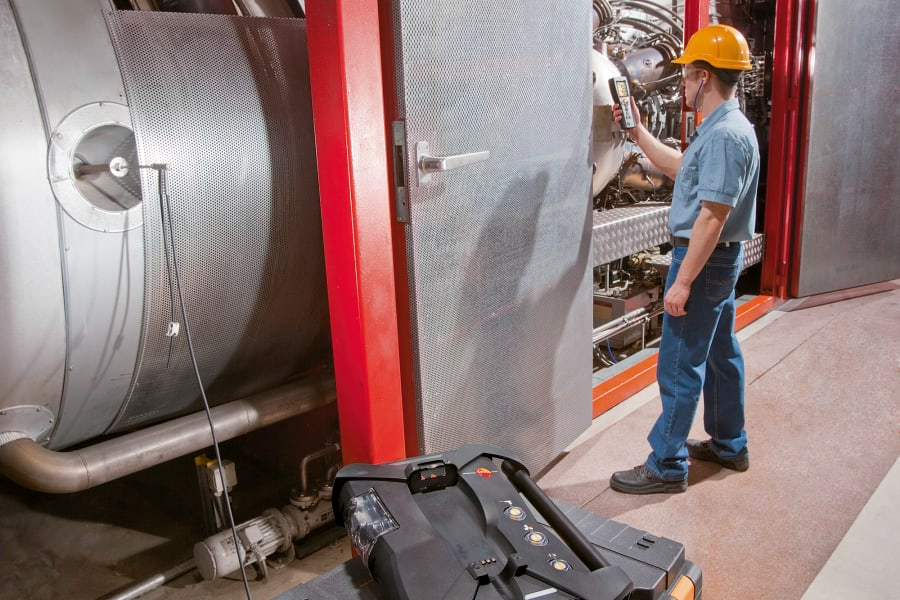



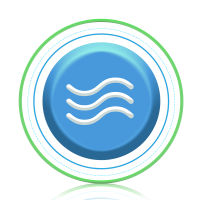
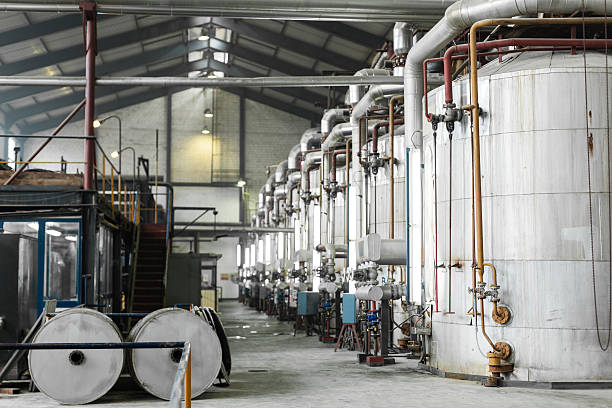
Process Equipment for the Petrochemical Industry
Bachiller develops a wide range of static and process equipment for the petrochemical sector, including solutions for reaction, filtration, vacuum drying, and mixing, while adhering to the industry’s most stringent quality standards.
The petrochemical industry is in charge of oil and natural gas treatment and transformation. Petrochemical plants employ a variety of chemical processes to produce a wide range of derivative products that are used in a variety of industries, including fertiliser, plastics, food, pharmaceuticals, chemical, and textiles.
Need a Consultation? Contact Us 24/7
Innovative Test & Measurement Solutions for Market Leadership