How Does An Oxygen Sensor Work?
Different industrial applications for quality control, process management, and environmental compliance all depend on oxygen sensors. Oxygen sensors measure the amounts of free oxygen in gases and liquids. Microorganisms are essential for degrading hazardous chemicals in liquid analytical applications, specifically wastewater treatment. These creatures typically need at least 5 ppm (parts per million) of dissolved oxygen to survive. For these processes to be healthy, it is essential to understand these levels. Analysing oxygen levels is crucial in many gas-based systems, especially those that employ nitrogen blanketing. Operators must make sure oxygen levels are kept to a minimum in these applications to prevent potentially disastrous reactions.
Temperature, water depth, salinity, bioactivity, and air pressure are just a few of the variables that affect oxygen levels. In order to effectively monitor oxygen in both gaseous and dissolved forms, it’s crucial to comprehend these variables. Let’s investigate how oxygen sensors function.
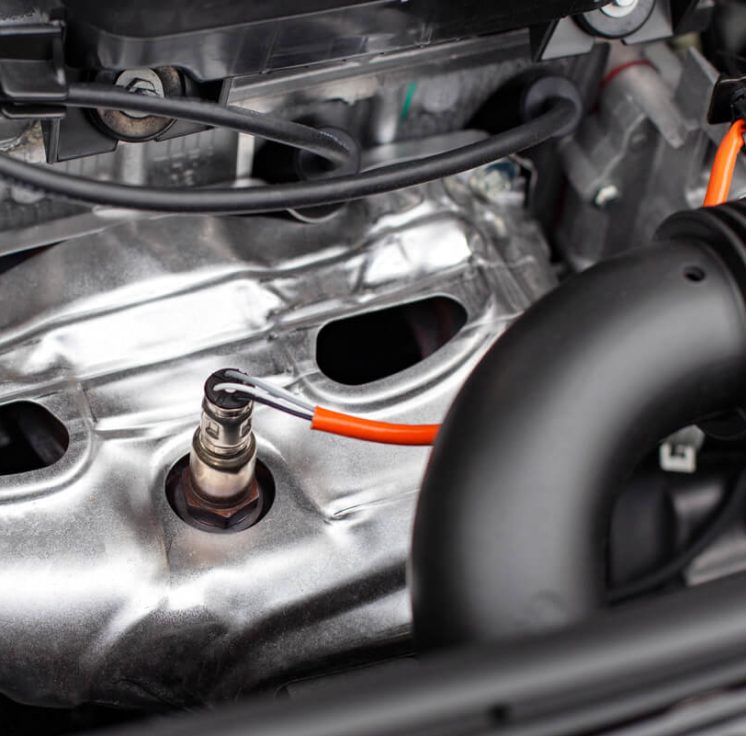
HOW OXYGEN SENSORS OPERATE
The two main types of oxygen sensor technologies are optical (luminescent) and electrochemical (Clark-Style/amperiometric). Both sensor types have characteristics that make them suitable for particular circumstances in different applications. We’ll look at how each type of sensor functions so you can decide which technology is most appropriate for your application.
ELECTROCHEMICAL SENSORS
Compared to luminous sensors, electrochemical sensors can read oxygen levels up to 45 ppm, a higher range. As a result, they are more suitable for demanding applications like chemical and water treatment.
The anode and cathode of these sensors are submerged in a reference electrolyte, and an oxygen-permeable membrane is linked to both of them. The anode and cathode must be polarised through a transmitter or similar power source in order to properly interpret the voltage. The cathode is often made of a precious metal that keeps the sensor’s polarisation stable. The oxygen crosses the membrane during in-process measurement. Anode and cathode register a voltage as a result of an electrochemical reaction that has finished in the electrolyte.
The generated current will increase as the oxygen levels rise. The voltage will subsequently be translated into a legible oxygen value via a transmitter.

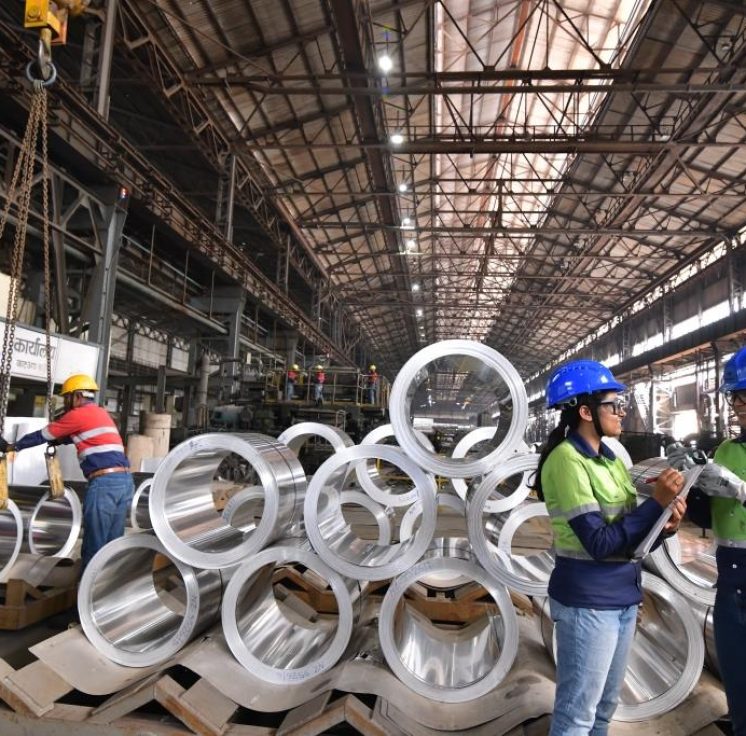
OPTICAL SENSORS
On the market, optical oxygen sensors are a relatively recent sensor type. These sensors are now being used more frequently in a variety of industrial processes thanks to technological advancements in this field.They work using an inside LED light and an external cap that has a fluorescent dye layer that is oxygen-sensitive. Additionally, a coordinated internal receiver converts light waves into readable oxygen levels. The wavelengths produced between the light and the dye layer will travel quickly to the transmitter in the absence of oxygen. The waves will move much more slowly after oxygen comes into contact with the dye layer.
MAINTENANCE IS KEY TO KEEPING SENSORS FUNCTIONAL & ACCURATE
The model of the sensor determines the specific maintenance procedures needed to increase sensor lifespan and guarantee correct measurements.
Electrochemical Maintenance: A little more upkeep is needed for electrochemical sensors than for luminescent ones. Users must polarise the reference system using a transmitter or similar power source, as was already described. The reference system may need to be stabilised for several hours. Regular cleaning of the anode and cathode is also necessary to prevent wear, especially on the precious metal cathode. If the reference system is not correctly maintained, readings will start to drift and measurements will be inaccurate.
Optical Maintenance: The condition of the exterior cap housing the dye layer is crucial for sustaining a luminous oxygen sensor. Long-term exposure to corrosive or other abrasive environments will cause the luminous dye layer to degrade. The wavelength patterns of the LED light will alter due to a broken dye layer, which will reduce measurement accuracy. However, damaged dye layer caps can simply be replaced without needing a new sensor altogether.
DISCOVER WHICH MODEL WORKS FOR YOU
Both types of oxygen sensors offer advantages that allow them to be used in a variety of applications that call for oxygen measurements. Examine our choices for oxygen sensors to see which one suits your process the best.